The Importance of PLC Maintenance in Electronic Components Distribution
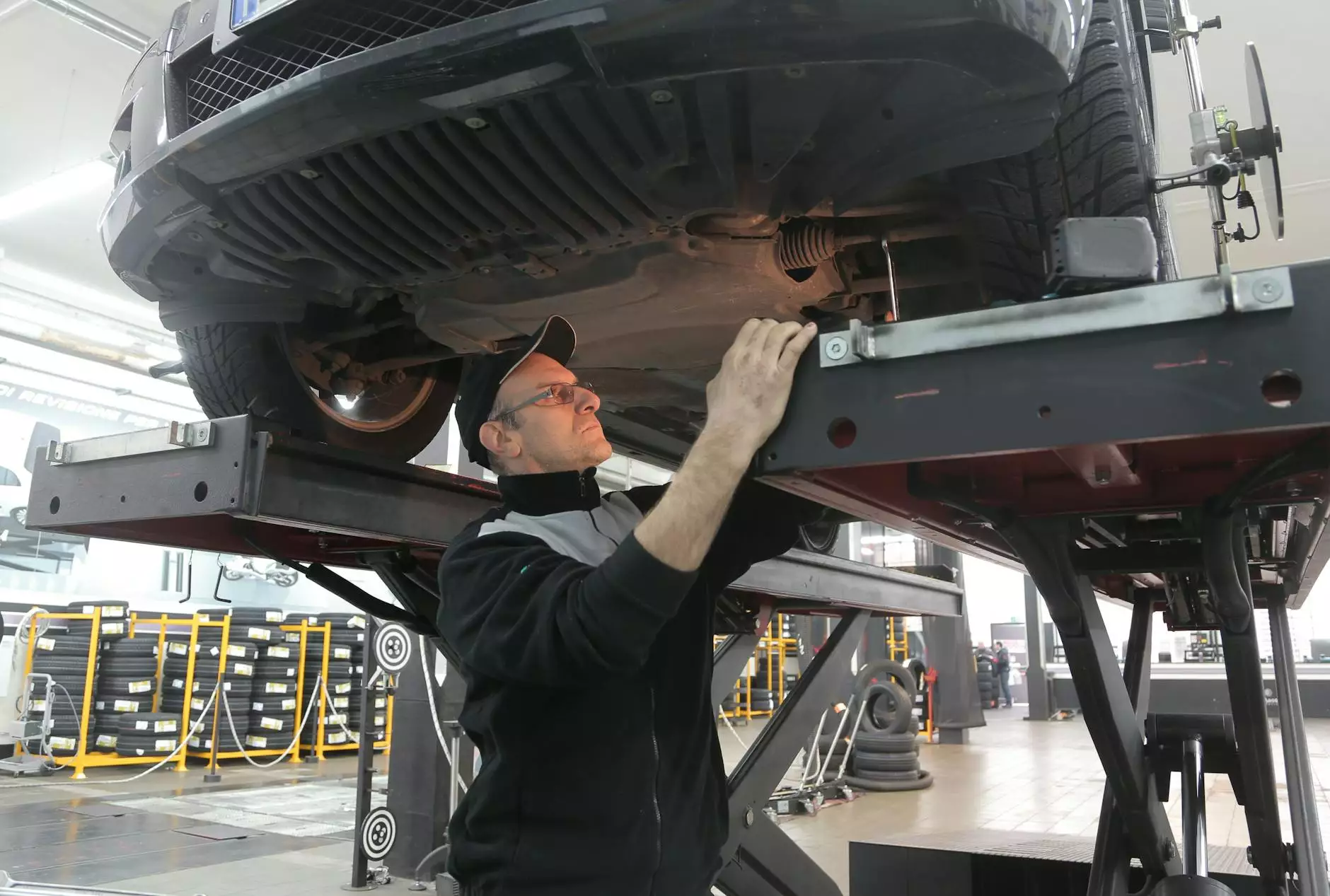
Understanding PLC Maintenance
PLC (Programmable Logic Controller) systems serve as the backbone of modern manufacturing and industrial operations. These devices control machinery and processes, ensuring everything runs smoothly and efficiently. However, like any advanced technology, PLCs require regular maintenance to avoid unforeseen issues. PLC maintenance encompasses a range of practices designed to ensure reliability, efficiency, and longevity of the equipment.
Implementing an effective maintenance strategy not only maximizes the operational uptime of these systems but also contributes to overall safety within the workspace. In this article, we will delve into the significance of PLC maintenance, the benefits of routine checks, and how businesses like qfautomation.com provide essential services for electronic components distribution and PLC repair services in Canada.
The Role of a Distributor in Electronic Components
The role of an electronic components distributor is vital in the industrial sector. Distributors provide a crucial link between manufacturers and end-users, ensuring that quality components are readily available to maintain and repair equipment like PLCs. With a good distributor, businesses have access to a wide range of products that are necessary for both new installations and ongoing maintenance.
Key Responsibilities of Electronic Components Distributors
- Product Sourcing: Identifying and sourcing high-quality electronic components that meet industry standards.
- Inventory Management: Keeping track of stock levels to ensure that essential components are always available for immediate use.
- Technical Support: Providing expert guidance on component selection and system integration for smooth operations.
- Logistics and Supply Chain Management: Ensuring timely delivery of components to minimize downtime in manufacturing processes.
Benefits of Regular PLC Maintenance
The importance of regular PLC maintenance cannot be overstated. Here are some key benefits:
1. Enhanced Operational Efficiency
Regular maintenance ensures that the PLCs operate at peak efficiency, reducing the likelihood of unexpected breakdowns that can halt production. By performing routine checks and updates, businesses can maintain optimal performance levels.
2. Prolonged Equipment Lifespan
Like any electronic equipment, PLCs have a finite lifespan. Routine maintenance helps identify and address potential issues before they become major problems. By investing in maintenance services, companies can extend the lifespan of their PLCs, resulting in significant cost savings.
3. Improved Safety
Faulty PLCs can lead to unsafe operational conditions, placing both employees and equipment at risk. By implementing a robust PLC maintenance schedule, companies can mitigate these safety risks, ensuring a secure working environment.
4. Compliance with Industry Standards
Various industries are held to specific compliance standards that ensure product quality and employee safety. Regular maintenance helps businesses adhere to these regulations, avoiding legal issues and enhancing their reputation.
5. Reduced Operational Costs
Unexpected breakdowns can lead to costly repairs and lost production time. Regular maintenance is a proactive approach that can significantly reduce operational costs by preventing major failures and unplanned downtime.
Common PLC Maintenance Practices
There are several essential practices involved in PLC maintenance. Implementing these can contribute to the longevity and reliability of your systems:
- Routine Software Updates: Ensuring that the software controlling the PLCs is current and functioning optimally.
- Regular Inspections: Conducting periodic inspections to check for physical damages, loose connections, or signs of wear.
- Calibration Checks: Regularly calibrating PLC systems to ensure accuracy in measurements and operational commands.
- Backup and Recovery Testing: Regularly backing up program files and testing recovery procedures in the event of a failure.
- Documenting Maintenance Activities: Keeping detailed records of maintenance activities helps track the history of repairs and updates.
How QFAutomation Addresses PLC Maintenance
As an established distributor of electronic components and provider of PLC repair services in Canada, qfautomation.com plays a crucial role in facilitating effective PLC maintenance. Here’s how they support businesses:
Expert Technical Assistance
The knowledgeable team at QF Automation offers technical support for all aspects of PLC operation, ensuring the systems run effectively.
Comprehensive Repair Services
With specialized PLC repair services, QF Automation can quickly respond to any breakdowns, minimizing downtime and keeping production lines running.
Quality Component Distribution
Their extensive inventory of high-quality electronic components helps businesses to procure everything needed for their PLC systems, from basic components to complex modules.
Customized Maintenance Plans
QF Automation offers customized maintenance plans tailored to the specific needs of each business, ensuring that all aspects of PLC maintenance are adequately addressed.
Conclusion
In the fast-paced world of industrial operations, effective PLC maintenance is critical to ensuring continuous productivity and safety. Electronic components distributors like qfautomation.com play a pivotal role in this process, offering essential services that help businesses optimize their systems.
By prioritizing routine maintenance, investing in quality components, and working with reliable distributors, companies can not only increase their operational efficiency but also secure their place in the competitive market. Remember, proactive maintenance is always better than reactive repairs—don't wait for a breakdown to realize the importance of proper PLC care.
© 2023 QF Automation. All rights reserved.