Understanding Pressure Measurement Units
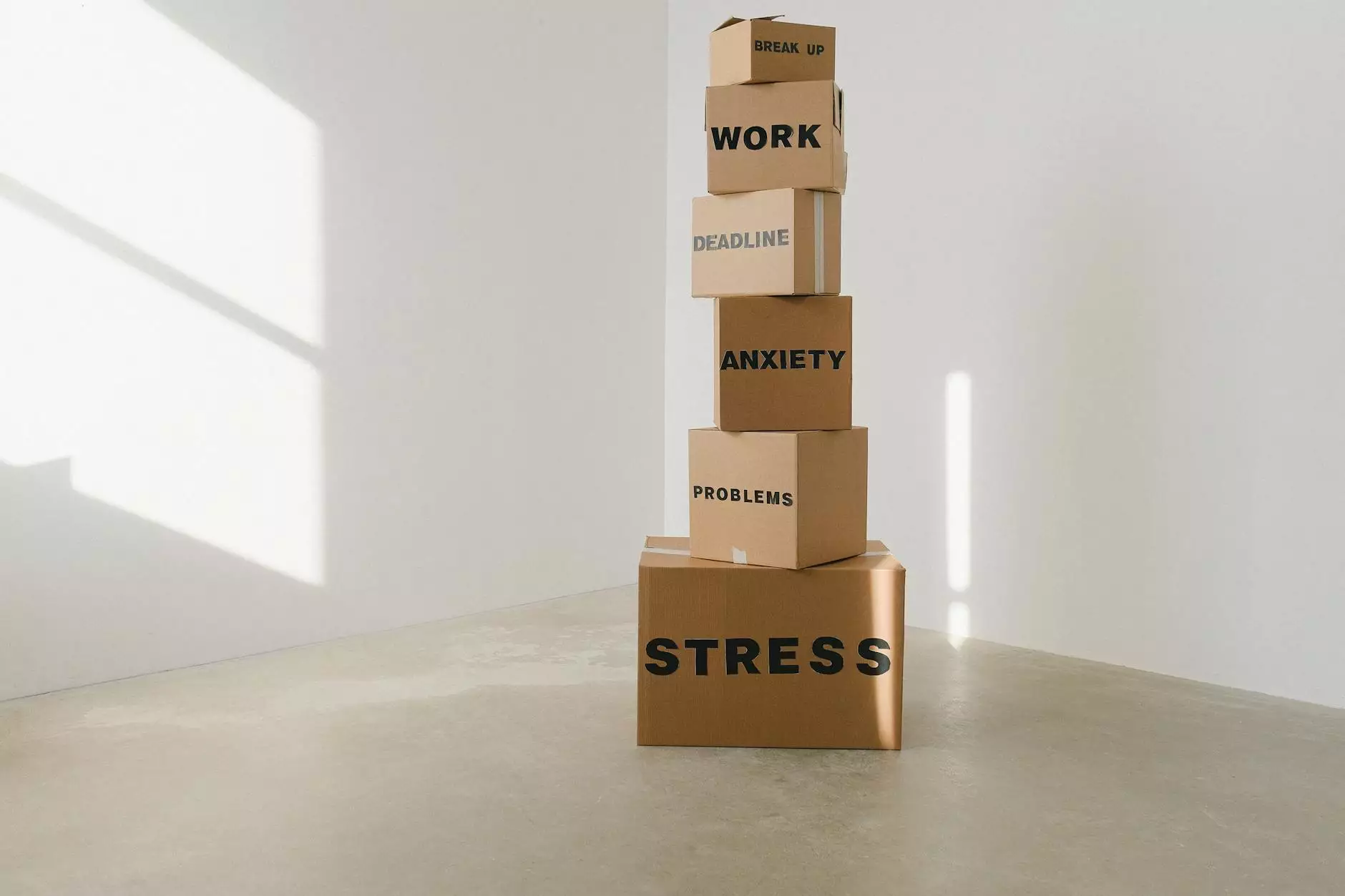
The Significance of Pressure Measurement in Engineering
In the fields of engineering, particularly within auto repair, farm equipment repair, and structural engineering, understanding what unit is pressure measured in is crucial. Pressure is a critical parameter that affects the performance and safety of various machinery and structures. Accurate pressure measurement ensures that systems operate efficiently and safely.
Pressure can be generally defined as the amount of force applied per unit area. This fundamental physical quantity is essential for a vast array of applications, from hydraulic systems to atmospheric studies. The ability to measure pressure accurately is vital for quality control, system design, and operational reliability.
Units of Pressure: A Comprehensive Overview
Different fields use various units to measure pressure, and familiarity with these units is essential for professionals in the engineering domain. Here are the most commonly used units of pressure:
- Pascals (Pa): The SI unit of pressure, defined as one newton per square meter. It is widely used in scientific contexts.
- Bar: A bar is equal to 100,000 pascals. This unit is commonly used in meteorology and industrial applications.
- Millimeters of Mercury (mmHg): This unit is often used in medicine and barometry, where it measures the pressure exerted by a column of mercury.
- Pounds per Square Inch (psi): Commonly utilized in the United States, especially in the automotive and agricultural sectors. One psi equals the pressure exerted by a force of one pound on an area of one square inch.
- Atmospheres (atm): Standard atmospheric pressure at sea level is defined as one atmosphere, equivalent to 101325 pascals.
- Torr: Similar to mmHg, this unit is commonly used in vacuum measurements and is defined such that 1 torr equals 1 mmHg.
Application of Pressure Measurement Units in Auto Repair
In auto repair, correct pressure measurement can significantly affect vehicle performance and safety. Several components rely on precise pressure readings:
- Tire Pressure: Measured in psi, proper tire pressure ensures optimal traction, fuel efficiency, and tire longevity. A properly inflated tire is crucial for vehicle safety.
- Brake Systems: Hydraulic brake systems depend on pressure; brake fluid pressure must be within specified limits to ensure proper function.
- Fuel Systems: Fuel injection systems rely on appropriately measured fuel pressure, typically in psi, to ensure efficient engine combustion.
Farm Equipment Pressure Measurement
For those involved in farm equipment repair, pressure measurement is equally vital. Agricultural machinery such as tractors and sprayers require precise pressure readings for optimal performance:
- Hydraulic Systems: Similar to automotive applications, hydraulic systems in farm equipment need precise pressure monitoring to ensure functional hydraulic components.
- Sprayer Pressure: Maintaining the correct pressure in spraying equipment is essential for effective pesticide or fertilizer applications.
- Irrigation Systems: Pressure measurement ensures proper water distribution in irrigation systems, which is vital for crop health.
Structural Engineering: The Role of Pressure Measurement
In structural engineering, pressure plays an important role, especially pertaining to static and dynamic loads. Understanding what unit is pressure measured in can affect design safety and structural integrity. Key applications include:
- Load Testing: Pressure sensors help in evaluating how structures handle loads, essential for ensuring safety standards are met.
- Fluid Pressure in Structures: Engineers must consider the pressure exerted by fluids in dam structures, pipelines, and related systems.
- Foundation Engineering: Monitoring soil pressure is critical for foundation design, ensuring structures remain stable over time.
Challenges in Pressure Measurement
While understanding what unit is pressure measured in is crucial, it’s also important to note the challenges that can arise in accurate pressure measurement:
- Calibration: Pressure gauges must be regularly calibrated to maintain accuracy. Environmental factors can lead to deviations that affect readings.
- Temperature Effects: Temperature changes can alter fluid properties, which may impact pressure readings, particularly in engineering applications that involve thermal processes.
- Mechanical Issues: Wear and tear in mechanical components may cause inaccuracies in pressure readings, necessitating routine maintenance.
Innovations in Pressure Measurement Technologies
Advances in technology have led to sophisticated methods of pressure measurement that enhance accuracy and ease of use. Some notable innovations include:
- Digital Pressure Meters: Digital gauges provide precise pressure readings and often come equipped with memory functions for data retrieval.
- Wireless Pressure Sensors: These sensors allow for remote monitoring and data collection, useful for real-time pressure management in large systems.
- Smart Sensors with IoT Integration: Many modern pressure sensors can connect to the Internet of Things (IoT), allowing for advanced data analytics and monitoring.
Conclusion: The Importance of Understanding Pressure Units
In the realms of auto repair, farm equipment repair, and structural engineering, accurately understanding what unit is pressure measured in is paramount. The significance of proper pressure measurement cannot be overstated, as it ensures safety, efficiency, and optimal performance in various engineering applications.
As technology advances, the tools available for pressure measurement will continue to evolve, offering more efficient and accurate means of ensuring the functionality and safety of engineering projects. It is essential for professionals in these fields to stay informed about the latest advancements and to maintain a deep understanding of pressure measurement principles.