The Rise of Silicone Injection Molding Machines in the Electronics and Medical Industries
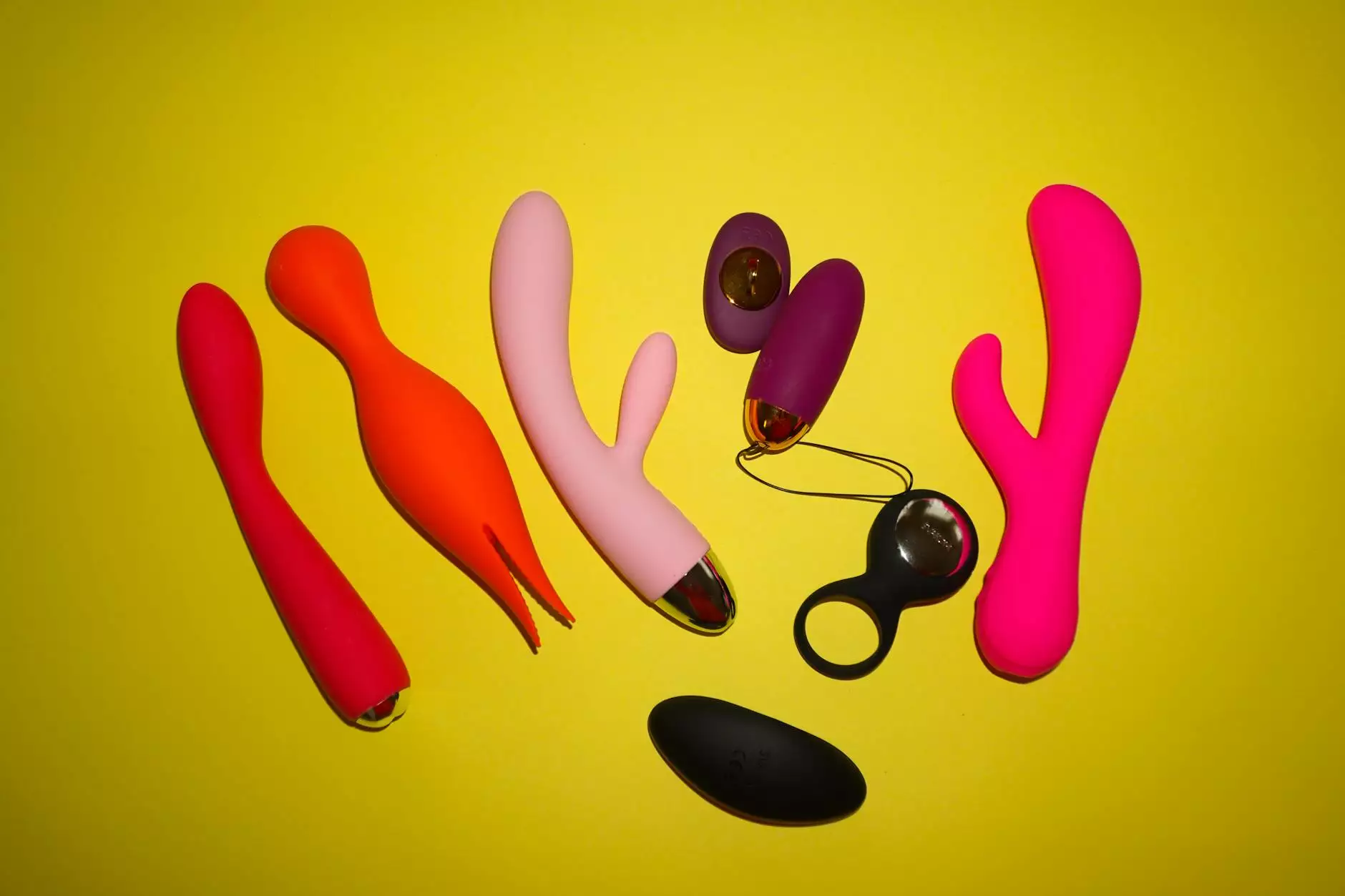
In today's rapidly evolving technological landscape, silicone injection molding machines have emerged as a cornerstone in the manufacturing processes of various industries, particularly in the realms of electronics and medical supplies. These advanced machines offer unparalleled precision and versatility, enabling businesses to produce high-quality silicone products that meet the stringent demands of modern consumers.
The Importance of Silicone in Manufacturing
Silicone, a synthetic polymer, is renowned for its exceptional properties, which include:
- Heat Resistance: Silicone can withstand extreme temperatures, making it ideal for applications where thermal stability is crucial.
- Flexibility: Its inherent flexibility allows for the creation of complex shapes and designs.
- Durability: Silicone materials are highly resistant to aging, UV radiation, and weathering.
- Biocompatibility: Medical-grade silicone is safe for use in medical applications, ensuring patient safety and compliance with health regulations.
These properties make silicone an attractive choice for manufacturers in sectors where performance and reliability are non-negotiable. Companies like Nolato are leveraging these advantages to create innovative products that cater to diverse market needs.
The Role of Silicone Injection Molding Machines
Silicone injection molding machines play a pivotal role in the molding of silicone products. They offer various benefits, including:
- Precision and Consistency: These machines are designed to deliver consistent results, ensuring that each product meets the exact specifications.
- Cost Efficiency: By reducing material waste and increasing production rates, the use of silicone injection molding machines leads to significant cost savings.
- Complex Geometry Capabilities: With advanced technology, these machines can create intricate designs that are challenging to achieve with traditional molding methods.
The combination of these advantages makes silicone injection molding machines indispensable for manufacturers striving to maintain competitiveness in a challenging marketplace.
Applications in the Electronics Industry
In the electronics sector, silicone injection molding machines are employed to produce a range of components, including:
- Encapsulation of Electronics: Silicone is used to protect sensitive electronics from moisture, dust, and impact.
- Cables and Connectors: Silicone provides excellent insulation and flexibility, making it ideal for wiring applications.
- Keypads and Switches: Soft-touch silicone keypads enhance user experience in various electronic devices.
These applications demonstrate how silicone injection molding machines contribute significantly to improving the performance and durability of electronic products.
Transforming the Medical Supplies Sector
The medical industry is another field where silicone injection molding has made a profound impact. The machines are vital in producing essential healthcare products such as:
- Medical Devices: Surgical tools and medical implants often utilize silicone because of its biocompatibility.
- Hospital Supplies: Items such as syringes and infusion systems benefit from silicone's durability and safety.
- Wearable Health Tech: Silicone is commonly used in wearable devices as it offers comfort and flexibility.
By ensuring that medical supplies are manufactured with high standards, silicone injection molding machines uphold the health and safety of patients worldwide.
Technological Advancements in Silicone Injection Molding
With ongoing research and development, the capabilities of silicone injection molding machines continue to expand. Recent technological advancements include:
- Automation: Automated systems enhance production speeds and reduce labor costs, promoting efficiency in processing.
- Smart Manufacturing: The integration of IoT technology allows for real-time monitoring and predictive maintenance, ensuring machines operate at peak performance.
- Green Technology: Innovative systems are being developed to process bio-silicone, reducing the environmental impact of manufacturing.
These advancements not only support increased productivity but also pave the way for sustainable practices within the industry.
Choosing the Right Silicone Injection Molding Machine
When selecting a silicone injection molding machine, manufacturers need to consider several factors to ensure they make informed decisions:
- Production Volume: Assess your production requirements to choose a machine that can handle your expected output.
- Machine Specifications: Examine the technical specifications, such as injection capacity and clamping force, to guarantee compatibility with your product designs.
- Supplier Reputation: Partner with reputable suppliers known for quality machines and after-sales support like Nolato.
Investing in the right machinery maximizes operational efficiency and product quality.
The Future of Silicone Injection Molding Machines
As industries continue to evolve, the future of silicone injection molding machines looks promising. With trends indicating a shift towards customization and on-demand production, manufacturers must remain adaptable. The emphasis on sustainability, technological integration, and product innovation will shape the landscape of silicone manufacturing.
Companies such as Nolato are at the forefront of these changes, continually investing in technology that aligns with future market demands.
Conclusion
Silicone injection molding machines have solidified their place as an essential element in the manufacturing processes of the electronics and medical supplies industries. Their ability to produce high-quality, durable products makes them a key player in today’s market. By embracing the advancements in technology and focusing on quality, companies like Nolato are well-positioned to lead the charge into the future, ensuring they remain competitive in a dynamic and challenging environment.
In conclusion, silicone injection molding is not just a method; it's a gateway to innovation, quality, and sustainability across various sectors. As we move forward, the role of silicone and its processing technologies will undoubtedly expand, paving the way for new opportunities and advancements in the industrial realm.