Essential Guide to Lift Station Alarms for Optimal Safety
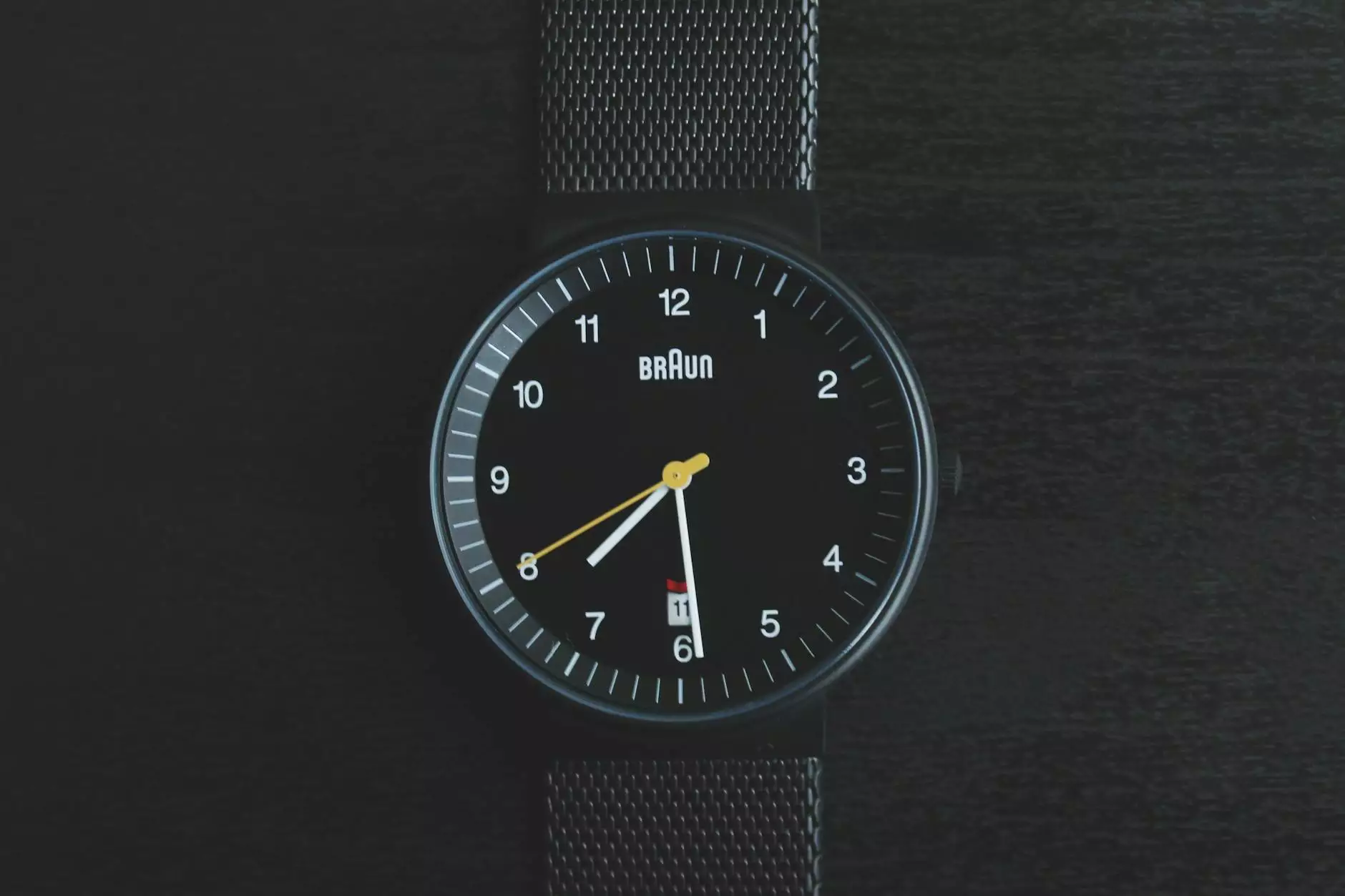
In the ever-evolving world of business, especially within the realms of Auto Parts & Supplies and Safety Equipment, one element that stands out as crucial yet often overlooked is the lift station alarm. These devices play an essential role in maintaining operational efficiency and ensuring safety in various industries, particularly in waste management. This article delves deeply into the significance, functionality, and benefits of implementing lift station alarms in business operations.
What is a Lift Station Alarm?
A lift station alarm is a critical monitoring system designed to alert operators of any anomalies within a lift station. It plays an integral role in maintaining wastewater management systems, where the elevation of liquids is necessary to prevent backups and flooding. These alarms provide real-time notifications regarding the status of pumping equipment, levels of wastewater, and more.
Key Functions of Lift Station Alarms
- Level Monitoring: Continuous assessment of wastewater levels to prevent overflow.
- Pump Status Monitoring: Alerts when pumps fail or require maintenance.
- Power Failure Notifications: Signals when there is a loss of electrical power to the lift station.
- System Alerts: Notifies operators of any unusual operational conditions that may require attention.
Importance of Lift Station Alarms in Business
The implementation of a lift station alarm is paramount for several reasons, particularly concerning safety and operational oversight:
1. Enhancing Safety Standards
Safety cannot be overstated in industries involving liquid waste management. A well-functioning lift station alarm ensures that operators are promptly informed of any potential hazards. Early detection of overflows or pump failures can mitigate risks to personnel and the environment. Businesses that prioritize safety through the use of effective alarm systems not only protect their employees but also uphold their reputation.
2. Minimizing Operational Downtime
Operational downtime can be costly. A robust lift station alarm system minimizes this risk by enabling quick responses to problems. With immediate alerts, operators can address issues before they escalate, ensuring continued flow and productivity. This reduction in downtime enhances overall operational efficiency, contributing to cost savings.
3. Compliance with Regulatory Standards
Many businesses are subject to stringent regulations regarding wastewater management. Proper installation and maintenance of lift station alarms align with these regulations, ensuring compliance and preventing potential legal repercussions. Staying ahead of regulations not only protects a business but also promotes sustainability within the community.
Components of a Lift Station Alarm System
A comprehensive lift station alarm system includes various components that work together to provide effective monitoring and control:
1. Alarm Panel
The alarm panel serves as the central hub, receiving signals from various monitoring devices and displaying system status indicators. It is essential for operators to have access to clear, concise information about the lift station's operational state.
2. Float Switches
Float switches are critical for level monitoring. When the wastewater reaches a predetermined level, the float switch activates, signaling the pump to turn on or off. This automation is vital in preventing overflows.
3. Vibration Sensors
These sensors monitor the mechanical condition of pumps. Excessive vibrations may indicate wear, misalignment, or other issues. Vibration sensors can notify operators of maintenance needs before failure occurs.
4. Visual and Audible Alarms
Effective alarms must include both visual indicators (like flashing lights) and audible alerts (such as horns or bells) to ensure that operators are notified quickly, even in noisy environments.
5. Remote Monitoring Capabilities
Modern lift station alarm systems incorporate remote monitoring features, enabling operators to receive alerts via smartphones or computers. This capability ensures that they can respond to issues promptly, even when off-site.
Installation Best Practices for Lift Station Alarms
To ensure optimal functionality, following installation best practices for lift station alarms is crucial:
1. Site Assessment
Before installation, a thorough assessment of the site is essential. Understanding the specific requirements and layout will inform the installation process and ensure compatibility with existing systems.
2. Selecting the Right Equipment
Choosing high-quality components is critical. Look for alarms that meet industry standards and offer reliable performance in harsh environments often associated with lift stations.
3. Professional Installation
While some businesses might consider DIY installations, enlisting professional services is advisable. Experts ensure that equipment is installed correctly and that all components work seamlessly together.
4. Regular Testing and Maintenance
After installation, ongoing tests and maintenance are vital to ensure that the lift station alarm operates as intended. Regular checks can identify potential issues before they lead to failure.
Choosing a Reliable Provider for Lift Station Alarms
As business owners seek the best solutions for safety and operational efficiency, selecting a reliable provider for lift station alarm systems is paramount. Here are tips for choosing the right supplier:
1. Evaluate Experience and Reputation
Consider providers with solid industry experience and positive customer reviews. A reputable provider will have a track record of quality installations and excellent customer support.
2. Comprehensive Product Offerings
A provider that offers a range of products will allow for tailored solutions that meet specific business needs. This flexibility can be crucial as technologies evolve.
3. Support Services
Look for suppliers who offer comprehensive support services, including installation, training, and ongoing maintenance. The right support can enhance the effectiveness of the lift station alarm systems.
Future Trends in Lift Station Alarm Technology
As technology advances, the landscape of lift station alarms will undoubtedly evolve. Here are some future trends worth watching:
1. Smart Technology Integration
The integration of smart technology, such as IoT (Internet of Things), will continue to enhance the capabilities of lift station alarms. Remote monitoring, automated diagnostics, and advanced analytics will improve maintenance and operational efficiency.
2. Enhanced Data Analytics
The use of data analytics in alarm systems will allow for predictive maintenance. Businesses will be able to anticipate failures and address issues before they result in costly downtime.
3. Environmental Monitoring
Future lift station alarms may incorporate environmental monitoring to assess groundwater levels and contamination. This added functionality will strengthen environmental compliance and safety protocols.
Conclusion
In conclusion, implementing a lift station alarm system is critical for businesses operating in industries like auto parts supply and safety equipment. These systems not only ensure compliance with regulations but also enhance safety, reduce operational downtime, and protect the environment. By investing in quality lift station alarms and maintaining them properly, businesses can secure a reliable wastewater management process, ultimately boosting their overall operational efficiency. As technology continues to advance, staying informed about the latest trends will further enable businesses to optimize their systems for the future.
For more information on high-quality lift station alarms and associated safety equipment, visit tankvitals.com today.